Most important factors that affect pumps
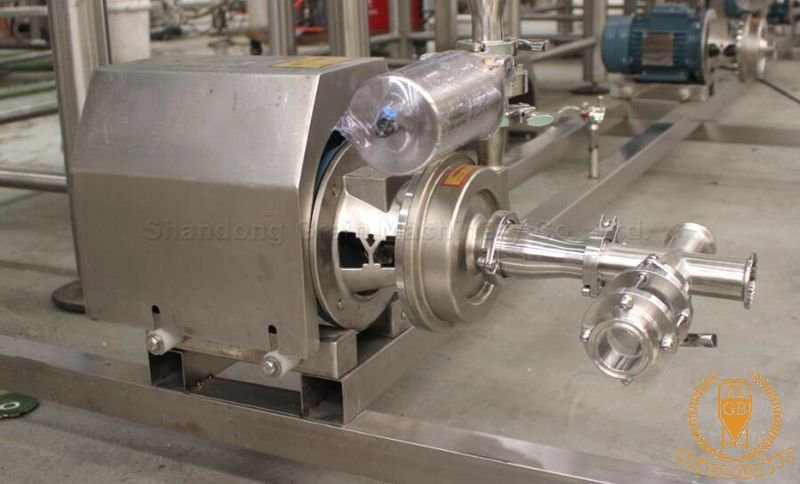
Q: What are the most important factors that affect pump sizing?
Flow rate: This can be chosen by the brewer based on required flow rates in the plant.
Pressure: This must be calculated based on the distance the pump must deliver the fluid on the discharge side.
It is important to consider the friction losses throughout the entire piping system, including elbows, tees and vertical height. Measured in PSI.
Viscosity: Viscosity is the resistance of liquid to flow. Centrifugal pumps are limited to lower viscosity fluids – like water or beer. Higher viscosity fluids require a PD pump.
Q: Why is my pump performing so poorly?
It may be running in reverse. This is a common mistake that is overlooked because centrifugal pumps will still produce flow in the correct direction even
when running in reverse but at a significantly reduced performance.
Q: Do mechanical seals in pumps allow oxygen into the system?
A mechanical seal is lubricated by the fluid being pumped, a thin film of the fluid is constantly slipping over the seal faces and generally vaporizes as it makes it across.
Even with a leaking seal, when the pump is running it is creating high pressure internally so fluid is pushed out of the leak and air will not go from the low pressure (atmosphere) to high pressure (pump).
If the pump is not running the CO2 pressure on the fermenter helps make sure that any leaks in pump or clamp connections are leaking from the system out to atmosphere rather than the reverse direction.
Even if there is not CO2 pressure on the fermenter the pump is many feet below the level of the fluid which creates a higher pressure than atmospheric pressure at the seal location.
Edit by Cody
[email protected]
Leave a Comment